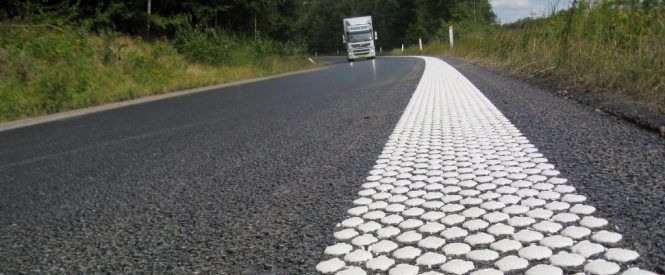
A Road Service Operator’s Process Documentation

In this quality management case study we have invited Lars Hauge the Quality Manager of the Danish road marking company “LKF Vejmarkering” to a talk about the company’s quality management, systems, quality assurance and process documentation. This case is a part of our series of quality management cases. All cases are based on interviews with Quality Managers.
Introduction to LKF Vejmarkering A/S and Lars Hauge
LKF Vejmarkering A/S LKF Vejmarkering A/S was founded in 1963. The company produces and applies plastic wrap to create road markings and lane stripes. Today LKF has offices all over Denmark and sales in more than 15 European countries.
Lars Hauge is the company’s Quality Manager. His entry to the field was somewhat unusual. At first, he worked at the company laboratory and then became a department manager. Here he found that the job mostly was about documentation and quality control. With this in mind, Lars took a Lead Auditor education and has now worked as a Quality Manager at LKF Vejmarkering for nine years.
A quality system mostly in the minds of the employees
At LKF roles, processes are not used very widely. Instead, they have a more informal approach as many of the employees have been with the company for many years. Most of the work at LKF is based on peer-to-peer training.
Peer-to-peer training is necessary due to a lack of formal rules and processes and as there is no formal training available for the industry. LKF is therefore forced to let peer-to-peer training be the main knowledge transfer tool. Their process documentation and quality assurance include some text-based descriptions of work procedures, which Lars is in charge of. Each procedure outlines who is responsible and it has descriptions of inputs and outputs.
Lars explains:
“It is hard to create instructions – it is learning by doing. We would maybe subsequently be able to make an instruction that could be learnt while working, but you would not be able to work solely from an instruction.”
We asked Lars if there are any special procedures to get new employees into the work?
No not really. We are working towards creating more instructions and process documentation. Due to the company’s startup in 1963, there are employees who have been with us for many years. They are starting to retire so there is a need for more process documentation in the future”
Maintenance of LKF’s Process Documentation
It is Lars’ responsibility to manage and maintain the overall process documentation and quality assurance. Other employees update the content itself. At least in theory. Process documentation is reviewed regularly. This is done by asking, “Does this still reflect the actual work process? Or do we need to adjust?“. The system they use for work is available via a shared file drive, giving access to everyone.
We asked if this is sufficient and Lars explained:
“The system we have today is only adequate in an ideal world”.
In reality, there are some problems. The current system hasn’t changed during the last nine years. With Lars’ own words it needs: “a thorough review”. Another problem with the current system is that it is difficult to maintain since it requires access to the source files when something needs to change. This means that you e.g. have to access the source code to insert a page break. This does not only make the maintenance process cumbersome but it also requires that Lars is involved for every update. But what if there is a need for change when Lars is not present? This is why LKF is about to change from a shared file drive to Sharepoint. The main expectation to SharePoint is to ease the maintenance and ensure that all employees easily can create process documentation and adapt tasks by using work descriptions.
Challenges of Quality Assurance
We asked Lars about his challenges as a Quality Manager. One of the challenges has been to encourage quality to be looked at by everyone, not just the quality department. He described one specific happening in the beginning of his career. During a management meeting, he talked about quality goals and some of the managers responded: “Surely we can find something”. This made Lars conclude that:
Then we might as well end it here since it hasn’t been understood what quality is all about.”
He explains that LKF today prioritise quality as part of the management agenda, but one of the current challenges is to develop a familiar and efficient strategy. A strategy that reflects the quality and supports the main strategy with quality goals: “There’s still an attitude about quality goals being a thing we do and then the main strategy run by itself – because it is where the money is made.”
We asked Lars how he accommodates this challenge. He explained that since he is a part of the management, he’s been able to emphasise how quality is an essential part of it, and today he sees a great improvement towards prioritising quality. Lars explained it was difficult to change the company’s view on quality since the management has the same members as it did when it became ISO certified in 1992. The challenge was to get the management to realise that the ISO 9001 has changed – from being based on written rules and signatures to a focus on what is important in the ISO-standard in terms of quality work.
The challenge of reaching the road
Lars explained that LKF is building upon the quality of their work and he knows that all employees have this in mind while performing their job. Therefore he does not focus on being in the field in relation to quality management. He explained that LKF has some talented middle managers in the field that focus on quality, which also is positive for the dissemination of quality.
Lars explained that he is aware that the knowledge about quality work should be available in the quality system. However, he also believes that if something works, you do not always have to explain why it is working. He does not think it is a necessity to involve all employees in the field of quality work – as long as everyone works within a framework and understands how the work should be performed. Furthermore, Lars explains that he daily spends the time talking to people in the company since he as the Quality Manager carries the audit-cap. Though Lars does not only audit but also to talk to the employees when he sees a need.
Lars’ advice when starting Quality Management
We asked Lars about his advice when starting Quality Management:
I took a Lead Auditor education and I recommend it to get to know the standard and to get a thorough knowledge of it – into the smallest detail.”
He explained that the Lead Auditor has provided him with great knowledge to identify the specific purpose of the standard. Since he almost had to shape the whole system, the Lead Audit also provided him with a broad knowledge about how to begin.
Lars recommends that if you want a certification, you should as a start get familiar with the standard, identify which requirements it contains and how these should be fulfilled. Later on, you can look beyond the certification requirements to get a solid quality system. He also recommends that you clarify what current systems can and cannot do in terms of fulfilling the requirements in an ISO 9001 certification.
Future quality assurance work
We asked Lars what the future as a Quality Manager at LKF brings him:
There is no doubt that when you are ISO 9001 certified there’s always some on-going changes according to the standard. With a new version next year the focus will be on the new standard and the changes it entails. Among other things, the risk analysis and how to get the management to take more responsibility for the things going on.”
These are the words from Lars Hauge, the Quality Manager at LKF Vejmarkering A/S. Soon we’ll present another case with a new perspective.
Frequently Asked Questions
Before the introduction of Gluu’s process documentation tool, road service businesses primarily managed their documentation through traditional mechanisms such as paper-based methods, which were time-consuming and often led to oversights and errors. The transition to a digital system brought about significant improvements.
Gluu’s process documentation tool comes with several notable features that have directly contributed to the enhancement of business efficiency and customer satisfaction. One such feature is the integration of all processes in a single platform, enabling quicker access and streamlined workflow. The tool also ensures task clarity with defined roles, helpful in reducing duty overlaps and confusion. Moreover, it monitors performance metrics, offering vital insights that could be used to improve further.
The road service businesses were grappling with challenges related to redundancy, inefficiency, and a lack of clarity in their operations. Gluu’s solution directly addressed these issues by offering an integrated platform for efficient process documentation and management. The software’s ability to outline clear responsibilities and track performance metrics was instrumental in addressing the difficulty of role confusion and inefficiency, thus improving the overall productivity of these businesses.